While the girls are compiling their fashion month reports, I thought I'd do a quick tutorial on zippers. In the world of doll fashion where most designers use snaps, hooks and velcro, a dress with a zipper is a luxury item. It's not that they are difficult to put them in. The problem--and expense--lies in finding doll sized zippers. Not an easy task. And when you do find them---well....even though they are 1/6 the size of a normal zipper--they certainly are not 1/6 the price! Yes, they are small, but they are ever as complex as the real thing.
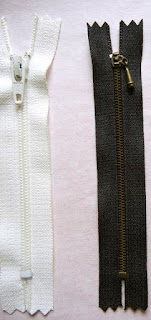
I have been to fabric and notions stores everywhere looking for 1/6 zippers. I will tell you now, you will have to order them online. For this post, I bought metal separating and metal regular zippers at I Sew For Dolls. (Located in the US, they ship fast. My order was perfect.) There are three other online sources that sell them as well. (Their websites are listed under Tutorials-Fab Favorite Resources.) Prior to buying 1/6 scale, I have to admit I've used 4"(10 cm) pant or jean zippers. They are the same length as doll size however, the teeth and zipper pulls are a bit large on the doll. The image above on the left shows the difference between human and doll zippers. On the right, the nylon zipper teeth are closer in scale, however the zipper pull is out-sized and I have yet to figure out how remove it! Nonetheless, the pant zipper is perfect for a 16" doll dress and will make do for the 12" doll inasmuch as it is sewn in the back which is out of view.
The Dress Zipper
Let's start with something simple. Whether you use a 1/6th zipper or a 4" (10cm) pant zipper, putting it in is the same.
1. Using a long, running stitch, baste the center back seam of your dress closed. No matter what happens, this ensures the zipper will line up perfectly with the center back seam of your dress.
2. Make sure the zipper is zipped shut and lay it face down against the seam of the dress. Leave a small space at the top of the dress (about 1/4" or 5mm) near the neckline.
3. Baste each side of the zipper to the corresponding side of the center back seam.
4. Working your way down one side of the back (about 1/8" (3mm) clear of the center back, stitch the zipper to the dress, using a tiny back-stitch. This is, in effect, a top stitch. (Note: You can also top-stitch using a sewing machine. Just be sure to use a zipper foot.)
5. When you get to where the zipper pull is, move it down a little then continue to stitch the zipper to the dress until you have finished. Repeat on the opposite side being care to create a line of stitches equally spaced from the center back seam.
6. You can finish the dress as you would normally. However, if you have gone through the trouble of buying zippers for your clothes, maybe you should consider putting in a lining! I've sewn my lining in as usual, leaving the space down the center back seam. I fold the lining's center back seams inward and pin so the bottom of the zipper is exposed and clear from the fabric. You want to get close to the zipper but far enough away so that the lining doesn't get caught.
7. I've hand stitched everything down. And at the top of the zipper---a hook and eye keeps it all closed and neat!
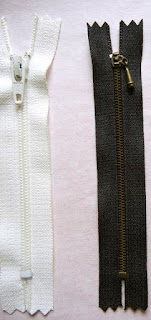
I have been to fabric and notions stores everywhere looking for 1/6 zippers. I will tell you now, you will have to order them online. For this post, I bought metal separating and metal regular zippers at I Sew For Dolls. (Located in the US, they ship fast. My order was perfect.) There are three other online sources that sell them as well. (Their websites are listed under Tutorials-Fab Favorite Resources.) Prior to buying 1/6 scale, I have to admit I've used 4"(10 cm) pant or jean zippers. They are the same length as doll size however, the teeth and zipper pulls are a bit large on the doll. The image above on the left shows the difference between human and doll zippers. On the right, the nylon zipper teeth are closer in scale, however the zipper pull is out-sized and I have yet to figure out how remove it! Nonetheless, the pant zipper is perfect for a 16" doll dress and will make do for the 12" doll inasmuch as it is sewn in the back which is out of view.
The Dress Zipper
Let's start with something simple. Whether you use a 1/6th zipper or a 4" (10cm) pant zipper, putting it in is the same.
1. Using a long, running stitch, baste the center back seam of your dress closed. No matter what happens, this ensures the zipper will line up perfectly with the center back seam of your dress.
2. Make sure the zipper is zipped shut and lay it face down against the seam of the dress. Leave a small space at the top of the dress (about 1/4" or 5mm) near the neckline.
3. Baste each side of the zipper to the corresponding side of the center back seam.
4. Working your way down one side of the back (about 1/8" (3mm) clear of the center back, stitch the zipper to the dress, using a tiny back-stitch. This is, in effect, a top stitch. (Note: You can also top-stitch using a sewing machine. Just be sure to use a zipper foot.)
5. When you get to where the zipper pull is, move it down a little then continue to stitch the zipper to the dress until you have finished. Repeat on the opposite side being care to create a line of stitches equally spaced from the center back seam.
6. You can finish the dress as you would normally. However, if you have gone through the trouble of buying zippers for your clothes, maybe you should consider putting in a lining! I've sewn my lining in as usual, leaving the space down the center back seam. I fold the lining's center back seams inward and pin so the bottom of the zipper is exposed and clear from the fabric. You want to get close to the zipper but far enough away so that the lining doesn't get caught.
7. I've hand stitched everything down. And at the top of the zipper---a hook and eye keeps it all closed and neat!
The Separating Zipper
Whereas you can probably get away with using a human sized 4" zipper to close the back of the dress, a separating zipper--that which is used for jackets--is another story! (If you attempt to use a regular zipper, the doll won't be able to get out of the jacket!) When you find a 1/6 separating zipper, it is a truly remarkable item worth the price. Fully functional and perfectly scaled, the doll jacket because a true miniature marvel. Putting this in is easy provided you remember to keep the zipper closed in the first few steps!
1. The material or fabric you use will determine the option you should chose. If you are working with a woven fabric that ravels at the edges, I would opt for the same instructions we used for the back zipper. But for this jacket, I am using python printed and stamped vinyl. Whether vinyl, plastic or leather, you don't have to worry about frayed edges but you do have to be concerned about bulk. So for this exercise, I am simply aligning the cut edge of the jacket against each side of the zipper. I pin the inside of the seams to the jacket.
2. Repeat on the other side, being careful that the two sides of the jacket line up perfectly.
3. Baste the jacket to the zipper. Check to make sure the zipper can move up and down smoothly without getting jammed.
4. If you are going to use a machine to top stitch this down, be sure to use a zipper foot. My machine is old, but your zipper foot will look similar to this. The zipper foot is more narrow than the regular one.
5. It is designed to hold the fabric/zipper down while leaving the needle free to stitch without obstructions. You can also elect to hand stitch this as we did with the dress zipper.
Waris can wear this jacket open and over a matching skirt. Or she can lend it to her girlfriend, Katoucha who wears it zipped up over pair of a silk abstract printed pair of trousers.
There are times, however, when putting in a zipper is more complicated. As an inspiration for my next project, I found a photo of a biker's jacket I wanted to make for my guys.
This was a bit of a challenge. The zipper is at a slight angle. The left lapel folds inward and the jacket zips up to the tip of the shoulder. Note how the zipper runs along one edge of the lapel but not the other. And to boot---it's all in leather!!!
This is a version of the pattern I used. Inasmuch as this is a tutorial on zippers, I decided to use a simplified version so as not to confuse you with umpteen pattern pieces. The principle for putting in the zipper, however, remains the same. The zipper is sewn into a seam on one side and is part of the lapel on the other. I cut (my) left side in two (blue line) and added seam allowance to both pieces. The zipper will lie against where you see the fuzzy green line. (The lapel folds over where you see the fold line.)
1. Using chalk, I drew in the seam allowance on the side front pattern. This provides a guide for the placement of the zipper.
2. I lightly press that line to further help me with my placement of the zipper.
3. In this instance, I open the separating zipper and place one side of it onto the side front panel. The teeth are facing inward--the seam allowance of the zipper placed along the seam of the side front jacket panel. I pin then baste the zipper onto the jacket (place pins on the seam allowance away from the stitch line). Even with lightweight leather, you will need to use a thimble.
4. My center front panel (which also has the lapel extension) goes on top and the zipper is sandwiched in the middle. I baste all three layers together using a long running titch. Basting keeps everything together as you sew the jacket together.
5. Now sew.
6. When you are finished and you turn the jacket to the right side up, the zipper teeth to the right.
6. Hammer the seams flat, being careful to avoid the zipper teeth.
7. Turn the left front and left side front right side out.
8. Zip the two sides of the zipper shut.
9. Place the right jacket front over the zipper and pin to the seam allowance. Carefully unzip the zipper and baste in place. Again, the zipper teeth should be facing inwards, away from the front edge.
10. Place the facing over the right jacket front with the zipper sandwiched in between and sew.
11. Clip the seam allowance around the tip of the lapel. Turn right side out. Use a pin to completely turn out the lapel tip. The zipper teeth should be now pointing outward towards the center front. Hammer the lapel flat.
12. Complete the jacket.
When All Else Falls, Fake It!
I could have stopped there, but you know me. There's always one more thing I want to try. What if....you are somewhere and those lovely doll zippers are not available. What if, your doll could care less about functionality and he (or she) simply wants the look of hardware.....
1. I started out by removing a metal zipper from an old, very decrepit pair of my dad's jeans. You can just go out and buy one if nothing is readily available. n any case, you should use a zipper that is color coordinated to the outfit you want to sew it in. Zip up the zipper so that the teeth are closed. Measure out the length you need and make a series of stitches around that point so the zipper won't unravel after you cut it. You need to do this at both ends.
2. Pin one side to the center front edge of the jacket.
3. Sew in place. On the other side of the zipper teeth, sew or glue a strip of velcro directly onto the zipper tape.
4. Add the other half of the velcro to the inside edge of the jacket.
The jacket can't be zipped up or down. The velcro holds it closed and simply gives the LOOK of a zippered jacket while allowing the doll to get in and out of it. And why not fake the look of zippered pockets!?!
1. This time, I took a bit of the zipper but left it open.
2. I placed each piece on the jacket for placement. When I have the placement I want, I used pins to indicate the line of the pocket.
3. On the inside, I mark those pin points with pencil. And connect the dots with a cutting line.
4. Using a blade or very sharp small scissors, slice open this line.
5. Now slide in the zipper sample.
6. This is how it looks right side up.
7. Stitch along the bottom of the opening.
If you try this out for your design, keep in mind you will need to allow for the extra space the zipper will take up in the front!
All text and photos property of Fashion Doll Stylist. Copyright 2018. Please ask permission before reposting. And please credit us. Thank you!
Follow us on Twitter: @FashDollStylist
Like us on Facebook: @FashDollStylist
We're also on Pinterest: @FashDollStylist
And of course, we are on Instagram: @fashiondollstylist
Whereas you can probably get away with using a human sized 4" zipper to close the back of the dress, a separating zipper--that which is used for jackets--is another story! (If you attempt to use a regular zipper, the doll won't be able to get out of the jacket!) When you find a 1/6 separating zipper, it is a truly remarkable item worth the price. Fully functional and perfectly scaled, the doll jacket because a true miniature marvel. Putting this in is easy provided you remember to keep the zipper closed in the first few steps!
1. The material or fabric you use will determine the option you should chose. If you are working with a woven fabric that ravels at the edges, I would opt for the same instructions we used for the back zipper. But for this jacket, I am using python printed and stamped vinyl. Whether vinyl, plastic or leather, you don't have to worry about frayed edges but you do have to be concerned about bulk. So for this exercise, I am simply aligning the cut edge of the jacket against each side of the zipper. I pin the inside of the seams to the jacket.
2. Repeat on the other side, being careful that the two sides of the jacket line up perfectly.
3. Baste the jacket to the zipper. Check to make sure the zipper can move up and down smoothly without getting jammed.
4. If you are going to use a machine to top stitch this down, be sure to use a zipper foot. My machine is old, but your zipper foot will look similar to this. The zipper foot is more narrow than the regular one.
5. It is designed to hold the fabric/zipper down while leaving the needle free to stitch without obstructions. You can also elect to hand stitch this as we did with the dress zipper.
Waris can wear this jacket open and over a matching skirt. Or she can lend it to her girlfriend, Katoucha who wears it zipped up over pair of a silk abstract printed pair of trousers.
There are times, however, when putting in a zipper is more complicated. As an inspiration for my next project, I found a photo of a biker's jacket I wanted to make for my guys.
This was a bit of a challenge. The zipper is at a slight angle. The left lapel folds inward and the jacket zips up to the tip of the shoulder. Note how the zipper runs along one edge of the lapel but not the other. And to boot---it's all in leather!!!
This is a version of the pattern I used. Inasmuch as this is a tutorial on zippers, I decided to use a simplified version so as not to confuse you with umpteen pattern pieces. The principle for putting in the zipper, however, remains the same. The zipper is sewn into a seam on one side and is part of the lapel on the other. I cut (my) left side in two (blue line) and added seam allowance to both pieces. The zipper will lie against where you see the fuzzy green line. (The lapel folds over where you see the fold line.)
1. Using chalk, I drew in the seam allowance on the side front pattern. This provides a guide for the placement of the zipper.
2. I lightly press that line to further help me with my placement of the zipper.
3. In this instance, I open the separating zipper and place one side of it onto the side front panel. The teeth are facing inward--the seam allowance of the zipper placed along the seam of the side front jacket panel. I pin then baste the zipper onto the jacket (place pins on the seam allowance away from the stitch line). Even with lightweight leather, you will need to use a thimble.
4. My center front panel (which also has the lapel extension) goes on top and the zipper is sandwiched in the middle. I baste all three layers together using a long running titch. Basting keeps everything together as you sew the jacket together.
5. Now sew.
6. When you are finished and you turn the jacket to the right side up, the zipper teeth to the right.
6. Hammer the seams flat, being careful to avoid the zipper teeth.
7. Turn the left front and left side front right side out.
8. Zip the two sides of the zipper shut.
9. Place the right jacket front over the zipper and pin to the seam allowance. Carefully unzip the zipper and baste in place. Again, the zipper teeth should be facing inwards, away from the front edge.
10. Place the facing over the right jacket front with the zipper sandwiched in between and sew.
11. Clip the seam allowance around the tip of the lapel. Turn right side out. Use a pin to completely turn out the lapel tip. The zipper teeth should be now pointing outward towards the center front. Hammer the lapel flat.
12. Complete the jacket.
When All Else Falls, Fake It!
I could have stopped there, but you know me. There's always one more thing I want to try. What if....you are somewhere and those lovely doll zippers are not available. What if, your doll could care less about functionality and he (or she) simply wants the look of hardware.....
1. I started out by removing a metal zipper from an old, very decrepit pair of my dad's jeans. You can just go out and buy one if nothing is readily available. n any case, you should use a zipper that is color coordinated to the outfit you want to sew it in. Zip up the zipper so that the teeth are closed. Measure out the length you need and make a series of stitches around that point so the zipper won't unravel after you cut it. You need to do this at both ends.
2. Pin one side to the center front edge of the jacket.
3. Sew in place. On the other side of the zipper teeth, sew or glue a strip of velcro directly onto the zipper tape.
4. Add the other half of the velcro to the inside edge of the jacket.
The jacket can't be zipped up or down. The velcro holds it closed and simply gives the LOOK of a zippered jacket while allowing the doll to get in and out of it. And why not fake the look of zippered pockets!?!
1. This time, I took a bit of the zipper but left it open.
2. I placed each piece on the jacket for placement. When I have the placement I want, I used pins to indicate the line of the pocket.
3. On the inside, I mark those pin points with pencil. And connect the dots with a cutting line.
4. Using a blade or very sharp small scissors, slice open this line.
5. Now slide in the zipper sample.
6. This is how it looks right side up.
7. Stitch along the bottom of the opening.
If you try this out for your design, keep in mind you will need to allow for the extra space the zipper will take up in the front!
All text and photos property of Fashion Doll Stylist. Copyright 2018. Please ask permission before reposting. And please credit us. Thank you!
Follow us on Twitter: @FashDollStylist
Like us on Facebook: @FashDollStylist
We're also on Pinterest: @FashDollStylist
And of course, we are on Instagram: @fashiondollstylist